Maintenance Manager
Career
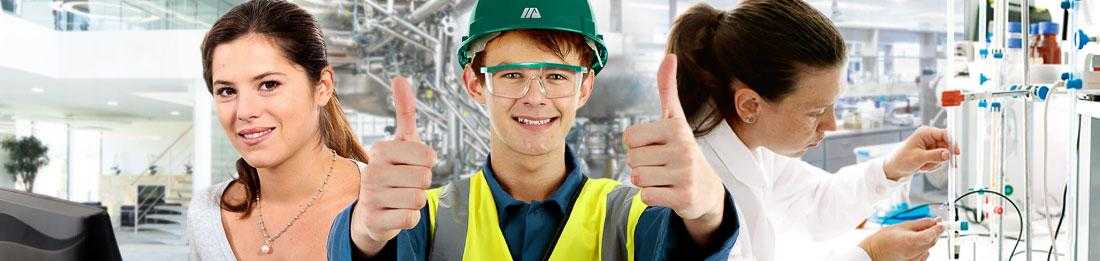
Maintenance Manager
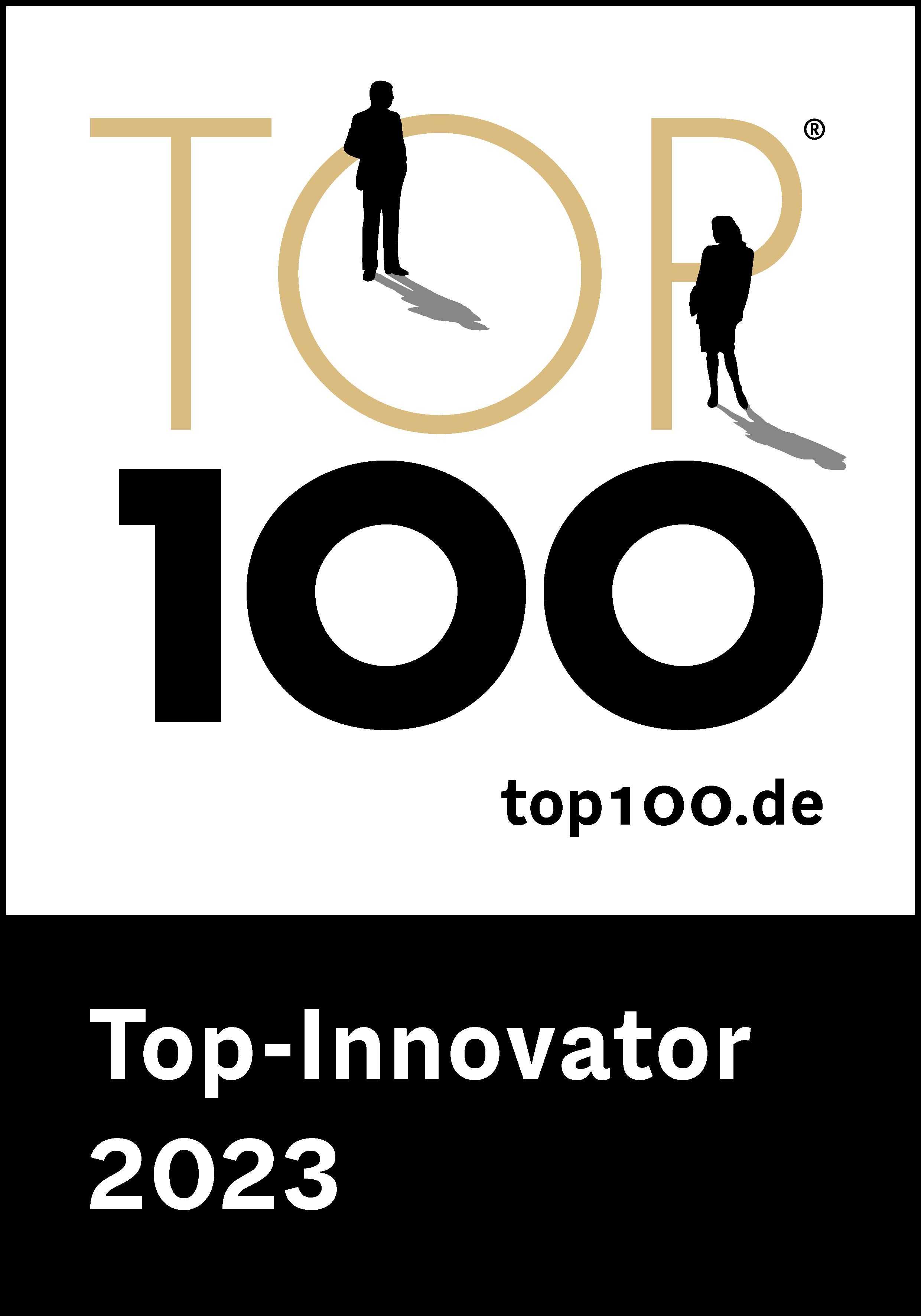
BASIC JOB FUNCTION:
The Maintenance Manager is responsible for the day-to-day oversight and maintenance of all plant operating equipment, and facility buildings. Monitors and maintains the efficient operation of equipment and facility, with safety and good housekeeping as a priority.
RESPONSIBILITIES:
•Works with supervisors/managers to plan work priorities, obtain necessary supplies, and assess skills needed to complete tasks
•Engages with team members to discuss upcoming work assignments; delegates assignments based on team member(s) skills and experience
•Oversees and evaluates maintenance department team and ensure ongoing training and development of all team member skill sets
•Manages preventative and predictive maintenance program to ensure maintenance costs are minimized while tracking reliability improvements
•Conducts root-cause failure analysis on component and critical equipment failures to include resolution and corrective action implementation
•Provides technical support and training to maintenance team and production personnel on component and critical equipment issues and solutions
•Responsible for preventive maintenance for systems and equipment. Schedule target dates for restoration/repair/replacement of inoperative components and parts
•Develops and maintains working relationships with current contractors/vendors/service providers and evaluates the marketplace for new contacts as needed
•Understands upkeep of electro-mechanical equipment such as pumps, motors, gear boxes, agitators, shrink wrap machines, etc.; and all utilities such as boilers, chillers, air compressors and wastewater systems
•Ensures maintenance and repair work is completed safely, effectively, and in a timely manner; and completes all work instructions / orders and forms
•Maintains electronic maintenance records for site (preventative maintenance, equipment files, and work order system)
•Complies with all plant safety rules, mechanical integrity procedures and plant maintenance procedures. Attends & participates in team safety meetings & site safety programs
SKILLS / ABILITIES:
•Ability to manage multiple projects/tasks and adjust priorities as necessary
•Must have good verbal and written communication skills
•Excellent analytical and problem-solving skills
•Ability to identify issues and to determine necessary repairs Ability to plan maintenance schedules for plant/building systems
•Demonstrates supervisory and leadership skills
•Proficient with Microsoft Office Suite or related software to complete reports, logs, & inventory
•Ability to maintain computerized maintenance system
EDUCATION & EXPERIENCE:
•Bachelor’s degree in engineering or related field (Mechanical or Chemical)
•Minimum 2-5 years’ experience working in a chemical plant with an emphasis on plant equipment or project management with a preference to previous maintenance supervision experience
•Prior experience in maintenance engineering with an emphasis on chemical compatibility, equipment failure analysis and system troubleshooting
•Prior experience reading schematics, plant and equipment drawings preferred
•Training and working knowledge of project management concepts
• Prior experience using computerized maintenance management software
PHYSICAL REQUIREMENTS:
•Ability to work an eight (8) hour shift in a chemical manufacturing and warehouse environment
•Ability to frequently lift and move items up to 50 lbs.
•Must be able to constantly move within and around exterior of the facility
•Occasionally ascends/descends ladder to perform maintenance responsibilities
• Ability to detect and recognize alarms/warning signals
WORK ENVIRONMENT: The physical environment requires the employee to work both inside manufacturing and warehouse facility and outside in heat/cold, wet/humid, and dry/arid conditions. Frequently required to use personal protective equipment to prevent exposure to hazardous materials. Company operates under ISO practices and procedures.